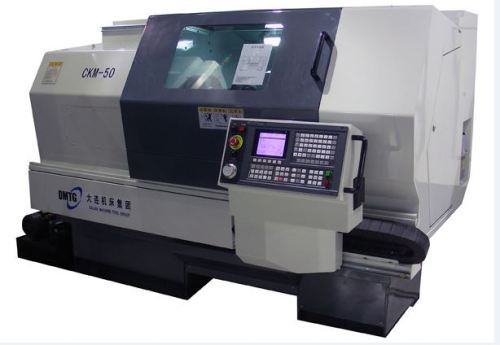
However, there are also some failures in the actual use of the machine tool. There is no alarm, and the phenomenon is not obvious. In this case, the processing is not as simple as it is well documented. In addition, after some equipment failures, there is not only no alarm information, but also lacks the necessary information for maintenance. If some machine tools fail to pay attention to the failure after use, some workpieces will be scrapped in batches, so it is more difficult to handle them. In the event of such failures, misjudgments are often made, resulting in unnecessary economic losses or extended repair times.
In addition, due to the fact that the frequency of failures is not high, the special maintenance service department will also encounter a lot of troubles when dealing with them. We think that such failures must be carefully checked according to the specific circumstances and analyzed from the tiny points of the phenomenon. Find out what it really is and try to solve it on your own.
Before you find the cause of a fault, you must understand the following: First, the fault occurs during normal operation or just after startup. Second, the number of occurrences occurs for the first time or several times. Third, confirm the machine tool's processing program will not be wrong. Fourth, whether other personnel have repaired or adjusted the machine. Fifth, whether there is any difference between the phenomenon of maintenance and the situation at the scene. The following is a brief analysis of some failures of CNC machine tools for reference.
CNC lathes appear to move manually during use, automatically return to zero after moving for a certain distance, and reopen manual movement is normal again. The lathe uses the economical numerical control, the stepping motor, moves by the speed when the manual movement is slightly slower, when the automatic zero returns, the fast movement distance is longer, appears the mechanical jam phenomenon. According to the failure analysis, the main reason is mechanical. After inquiry, it was learned that the machine tool was inaccurate in size due to machining. The fault occurred when the motor on the other machine was used for demolition. After careful inspection, it was due to transmission. The gear gap in the gear is too small and normal after re-adjustment.
The spindle is out of control. The spindle rotates without power and is accompanied by abnormal sound. Depending on the observed phenomenon, the cause of the failure may be the loss of control of the spindle controller and the cause of the mechanical transmission or motor cannot be excluded. Due to the large amount of work involved in the inspection of the dismantling machinery part, the spindle controller of the electric part is inspected. The preset parameters in the controller are checked first, and then the control pull is checked. No abnormality is found. The circuit board is dirty and the circuit board is pressed. It is required to clean the circuit board, but the power-on failure will still occur after it is installed. Therefore, the cause of the fault in the controller can be temporarily eliminated.
In order to determine whether the fault must be disengaged from the motor or the machinery in the motor or in the mechanical transmission part, the abnormal sound may be caused by a bearing defect after analysis. Remove the motor for inspection and find that the bearing has been damaged. After checking the encoder, the CD has been scratched and all the faults have been eliminated after replacing the bearing and encoder. This fault is mainly caused by an abnormal sound when the spindle rotates. Therefore, when troubleshooting, check the sound source and check it again. Abnormal sound is usually mechanical friction, jamming and bearing damage.
Faults in CNC machine tools are mostly difficult to handle. Among these failures, more are caused by mechanical reasons. Followed by some comprehensive factors caused by the failure, these failures are usually due to the power supply voltage, hydraulic, pneumatic, oil, environmental temperature and other external conditions. In addition, after the NC machine tool is used for a long time, due to the aging of components and the wear of mechanical parts, it will also cause problems in the matching between the system and the mechanical parts, which will lead to failure. The repair of these faults generally has a certain degree of difficulty, especially the judgment of the fault phenomenon is particularly important. Therefore, paying attention to the use environment of CNC machine tools and strengthening the maintenance of CNC machine tools is the fundamental way to reduce the probability of applause and is an important means to ensure the normal operation of CNC machine tools.
Plastic Injection Moulding Machine:
1, Fully optimized hydraulic system, efficiency 10% higher than last series( Standard EK) .
2, Hydraulic parts from famous international manufacturers, ensure machine with reliable performance.
3, Conform to GB, CE, UL, KCS or other safety standard.
Plastic Injection Moulding Machine
Plastic Injection Moulding Machine,Vertical Plastic Injection Moulding Machine,Small Plastic Injection Moulding Machine
Ningbo Shuangma Machinery Industry Co., Ltd , http://www.bolemachinery.com