1 principle of ultrasonic flowmeter
The commonly used ultrasonic flowmeter has two principles: time difference method and Doppler method.
1.1 Principle of Time Difference Method
The ultrasonic signal is in the fluid, the signal propagation speed is fast and the propagation time is short at the time of the forward flow; the signal propagation speed is slow and the propagation time is long at the time of the reverse flow. There is a difference in the propagation time of the acoustic wave signal along the upstream and downstream directions in the fluid using the ultrasonic signal, and the difference is instantaneous. Calculate fluid flow. The time difference method is more suitable for measuring pure liquids. A liquid or suspended substance with more bubbles will hinder the normal propagation of sound pulses, resulting in abnormal measurement.
1.2 Doppler principle
Ultrasonic signals are scattered on the propagation path with tiny floats (suspended matter or tiny bubbles), and the ultrasonic receiver can receive the scattered ultrasonic signals. The frequency of the transmitted signal is affected by the Doppler effect and becomes a different frequency of the received signal. The difference between the two frequencies has a definite quantitative relationship with the fluid flow rate, from which the fluid flow can be calculated. Doppler flowmeters cannot measure clean fluids and can only measure turbidity above about 50mg/L. At the same time Doppler measurement accuracy is lower than the time difference method, generally 2.0, that is, 2% full scale error (2% FS).
2 Ultrasonic Flowmeter Precautions
In recent years, with the increasingly widespread application of ultrasonic flowmeters in the online calibration of sewage flowmeters, the problem of low accuracy of flowmeters has gradually exposed, mainly due to non-standard operation and the flowmeter itself.
2.1 The operation is not standardized
On the pipeline side, technicians often do not operate in accordance with standard operating procedures, such as not accurately measuring pipe outside diameter, perimeter, wall thickness, contact temperature, etc. These parameters will have an important impact on the original data correction of ultrasonic flowmeters.
In terms of installation methods, technicians often do not select the installation method according to the pipe size and signal strength, and often choose the default dual sound path mode of the flow meter. The correct installation method is: single sound path should be adopted in large pipelines and complex environments; multiple sound paths should be selected when the small pipelines and signals are extremely strong.
In terms of installation location, technicians often place ultrasonic probes at random, and do not confirm whether the pipeline sewage is full or not, an important measurement condition. The correct installation position is: the probe should be placed in the horizontal middle position of the pipeline; the accurate measurement can only be performed under the condition that the pipeline is full, and the vertical pipeline of the fluid can ensure full flow.
In addition, important parameters such as the type and thickness of the pipeline lining on site are often difficult to obtain, and these also seriously affect the accuracy of the flowmeter.
2.2 Ultrasonic flowmeter problems
The first is the time difference method and Doppler flow meter selection. The time difference flowmeter is suitable for the measurement of pure liquid with an accuracy of better than ±1.0%. The Doppler flowmeter is suitable for fluids with turbidity above 50mg/L. Therefore, the selection of two kinds of principle flowmeters in the calibration of sewage flowmeters is very important. Under normal circumstances, when the sewage in the pipeline is relatively clean, the time difference method can be used; when the sewage is relatively turbid, the Doppler method should be used. However, the clean or cloudy sewage is difficult to be quantitatively defined on the site. Therefore, there is no universal method for the flowmeters that use these two principles, which leads to inaccurate measurement of the flowmeter itself, let alone calibration of the sewage flowmeter.
Secondly, there is also a flaw in ultrasonic reception. Ultrasonic waves are measured by transmitting and receiving ultrasonic signals in the pipeline to measure the fluid flow. Therefore, the refraction of the ultrasonic material by the pipeline material, the reflection and scattering of impurities in the fluid by the ultrasonic waves, and the content of the bubbles and impurities randomly present in the fluid will be measured. Has an erratic effect. Oilfield sewage contains a lot of crude oil, gravel, bubbles, chemicals, etc. The internal environment of the pipeline is very complicated and changeable, which seriously affects the accuracy of measurement.
The ultrasonic flowmeter is not accurate in the online calibration of the sewage flowmeter. In the past year, 26 sets of qualified sewage flow meters were used as reference flowmeters, and on-site on-line calibration was performed on 4 ultrasonic flowmeters. Through a large number of tests and data analysis, the flow rate of ultrasonic flowmeters was discussed. The role of calibration.
3.1 The choice of flow meter
In order to make the test representative, the portable ultrasonic flowmeter uses a time difference type A and a Doppler B type from a well-known foreign manufacturer, and the time difference type C and Doppler D type of each well-known domestic manufacturer are all qualified. In the verification period. 26 sewage flow meters are used for the first time after passing the test and are within the verification period.
3.2 Test Considerations
This test strictly follows the instructions attached to the ultrasonic flowmeter and the precautions mentioned in Chapter 3 of this article.
The straight pipe section of the pipeline installed by the flowmeter complied with the “first ten days and five yearsâ€. The pipeline chosen for the installation of the flowmeter in the test is a new pipeline within the last year, so as to avoid the problem that the ultrasonic signal receiving quality is not high due to the corrosion of the inner wall of the pipeline.
The design of middle through hole is easy to install, Barrel Damper is usually used in small spaces. ABD barrel dampers are the perfect solution for a wide range of applications. Barrel dampers are widely used in automobile interior decoration, household electric appliances, furniture, hidden socket, etc. Our dampers can make the movement of structures soft, quiet and safe to mitigate the impact, avoid the damage, increase the mechanical life, reduce noise, and improve product quality.
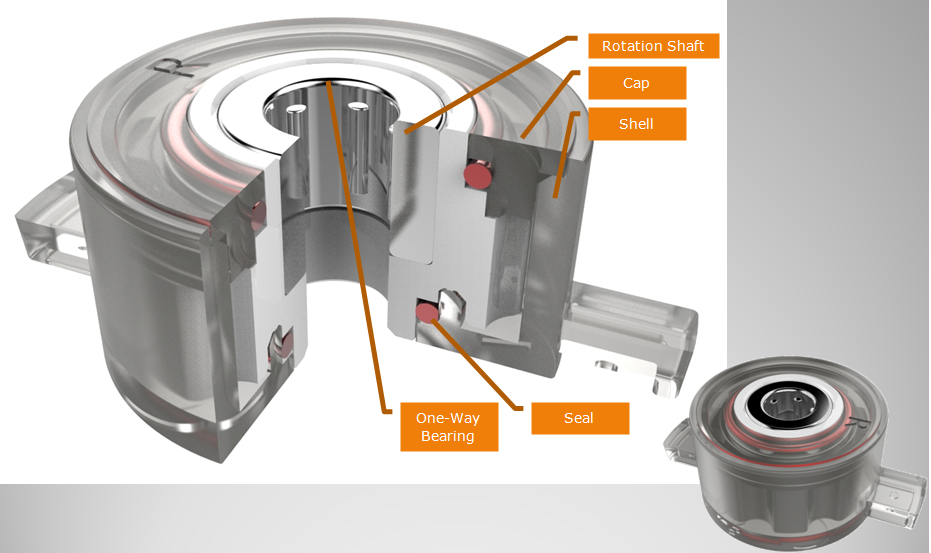
NOTE:
1. Please contact the corresponding product engineer for specific torque products.
2. Max. rotation speed: 50r/min
3. Max. circle rate: Clockwise180 °, 180 ° anti-clockwise for 1 cycle
4. Operating temperature: -10~50℃
5. Storage temperature:-30~60℃
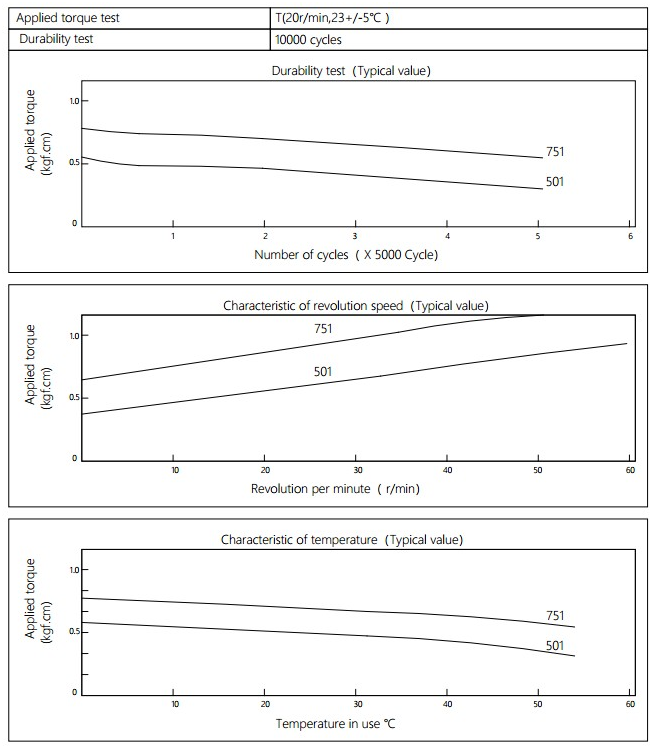
Applied torque:(T)
Test Temperature:23+/-5℃
Rotating speed:20r/min
Durability test Method:Clockwise 180 °, 180 ° anti-clockwise
Rotating speed:20r/min
Test Frequency:1cycle/min
Test Temperature:23±5℃
Durability test cycle:10000 cycle
Test result criteria: Store in the room temperature for 24 hours or more after the test, recording to the torque T=T±30%T.
Barrel Damper
Barrel Damper,Plastic Dampers,Manual Barrel Damper,Toilet Seat Damper,Plastic Barrel Rotary Damper
Shenzhen ABD Equipment Co., Ltd. , https://www.abddamper.com